BASF has now improved the process for manufacturing Lupranol® (polyether polyol) so that car components which are made of BASF polyurethane systems emit an average of 20 percent less aldehyde. This allows automotive suppliers, that manufacture e.g. acoustic parts, seats and steering wheels or back-foam instrument panels and doors, to meet the increasing requirements of car manufacturers and the law for lower emissions (VOCs: Volatile Organic Compounds) in vehicle interiors. Following the process change at BASF’s Asian production sites at the beginning of 2017, the modification is now being made in Europe and will take place in the US plants during the course of this year. Alongside isocyanate, polyol is the starting product for polyurethane foam systems.
BASF has now improved the process for manufacturing Lupranol® (polyether polyol) so that car components which are made of BASF polyurethane systems emit an average of 20 percent less aldehyde. This allows automotive suppliers, that manufacture e.g. acoustic parts, seats and steering wheels or back-foam instrument panels and doors, to meet the increasing requirements of car manufacturers and the law for lower emissions (VOCs: Volatile Organic Compounds) in vehicle interiors. Following the process change at BASF’s Asian production sites at the beginning of 2017, the modification is now being made in Europe and will take place in the US plants during the course of this year. Alongside isocyanate, polyol is the starting product for polyurethane foam systems.
The emissions have been optimized by improving the cleaning and finishing processes of Lupranol® in such a way that the mechanical properties of the material remain unchanged during the following foam and processing steps. This means that the currently used Lupranol® grades can be exchanged immediately, there is no need for elaborate tests or renewed approvals of the PU systems which are based on these improved polyol grades. BASF markets the PU systems for flexible, semi-rigid and integral foams under the trademarks Elastoflex® W, Elastoflex® E and Elastofoam® I.
With the improved Lupranol® grades BASF contributes to automotive components with ever lower emissions. Completed parts made of BASF PU systems are tested internally as well as by certified test laboratories like Imat-Uve and Institut Fresenius. The improvement of the emission values varies from part to part: An average reduction of 20 percent is possible, measured according to commonly accepted chamber test methods like VDA276 and BMW GS 97014-3.
Governments around the world are continuously demanding lower emissions for vehicle interiors in order to reduce the possible impact of volatile substances on the health of car drivers, but also to lessen the typical new-car smell. The focus is currently on aldehydes such as formaldehyde, acetaldehyde and propionaldehyde, as well as aromatics from polyurethanes. BASF is working intensively on developing PU systems which allow for car components with lower emissions.
Related Stories
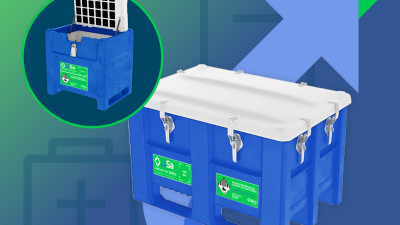
Call2Recycle and RLG Partner to Strengthen Battery Collection Safety with Innovative Technology
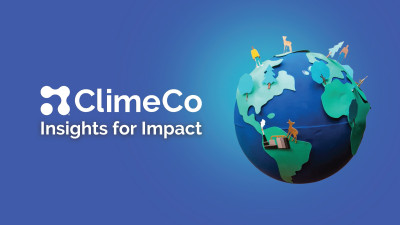
ClimeCo Announces "Insights for Impact" Video Series: Simplifying Decarbonization for All