New IBM technology turns PET into renewable resource
IBM researchers have created a new technology called VolCat, a catalytic
chemical process that can turn PET — a type of plastic commonly used in food
packaging and polyester clothing — into a renewable resource. The cost-effective
innovation is capable of breathing new life into old plastic.
With more than 272 million metric tons of plastic currently produced each year
(one-quarter of which is made up of PET), IBM Research’s VolCat chemical
recycling process aims to use a precise combination of chemicals, heat and
pressure to reduce this amount of plastic — and ultimately the amount of waste —
produced. This could completely transform the way we discard and manufacture
plastic in the next five years.
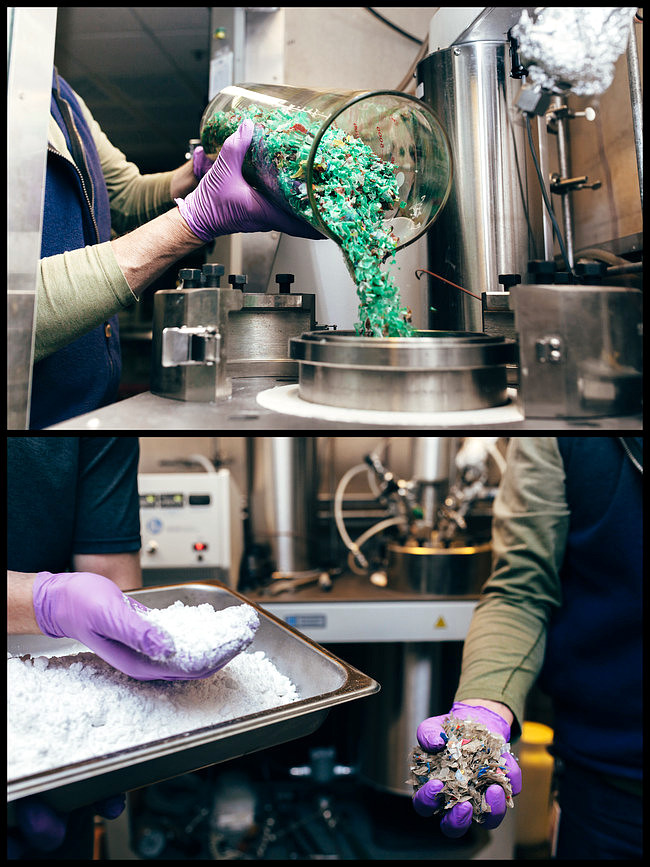
IBM Research’s VolCat chemical recycling process can make the most commonly used plastic polymer in the world, PET monomer (bottom left), out of mixed/dirty post-consumer waste (top photo). Unlike PET made from a mechanical recycling process, the VolCat-produced PET is 100 percent recyclable, giving it value far beyond its initial use and keeping our most common plastics in the recycling chain and out of the landfill. | Images credit: IBM
VolCat can make the most commonly used plastic polymer in the world, PET monomer
(bottom left), out of mixed/dirty post-consumer waste (top photo). Unlike PET
made from a mechanical recycling process, the VolCat-produced PET is 100 percent
recyclable, giving it value far beyond its initial use and keeping our most
common plastics in the recycling chain and out of the landfill.
“The catalyst finds the PET polymer and chews it up,” Bob Allen, senior
manager of chemistry and materials at IBM Research, said in a statement. “You
can visualize the polymer chains like a very long string of beads, and each bead
is a monomer unit. This catalyst goes in, kind of like a molecular pair of
scissors, and starts chopping it up very, very rapidly.”
The VolCat process is an alternative to traditional recycling, which usually
involves sorting waste, washing it, separating out contaminants, chopping up the
plastic and re-melting it, which creates lower-quality plastic that many
companies often don’t want to use. IBM’s process is one example of a growing
number of new methods for chemical recycling — such as BASF’s ChemCycling
project,
which uses thermochemical processes to break down plastics into syngas or oils
that the company is now using to partially replace fossil-based inputs in its
products.
TerraCycle helps Subaru of America recycle 1M pieces of plastic waste
Image credit: Subaru of America
Meanwhile, Subaru of America, Inc. announced this week that its dealerships
across the US have recycled one million pieces of waste through the
ongoing Subaru Loves the
Earth recycling program,
created in partnership with TerraCycle, a leader in the collection and
repurposing of complex waste streams.
"This milestone means a lot to us at Subaru because it reinforces our belief
that loving the environment means more than loving the great outdoors,"
said Alan Bethke, SVP of Marketing at Subaru of America, Inc. "Through our
partnership with TerraCycle, in less than a year, more than 540 participating
Subaru retailers located across the country have recycled more than one million
pieces of waste. This partnership allows Subaru owners and the communities that
our retailers serve to actively participate in preserving the environment and
making the world a better place."
Utilizing TerraCycle's Zero Waste Box™ platform, participating Subaru
retailers encourage customers, employees and community partners to recycle waste
streams that are commonly thought of as hard-to-recycle, including snack
wrappers; disposable cups and
lids;
and coffee, tea and creamer capsules. In addition, Subaru encouraged customers
to also collect these waste streams at their home or office and bringing them
into a local participating Subaru retailer.
The collected waste is then turned into useful, recycled products such as park
benches, picnic tables, and playground materials, and donated to Subaru
community partners. Subaru retailers can also view, and order products made from
the recycled materials through an exclusive Subaru product-line, produced in
conjunction with TerraCycle.
"At TerraCycle, we are committed to ensuring that waste continues to be diverted
away from landfills and local communities," said CEO Tom
Szaky. "Subaru not only shares that
commitment but has taken it to the next level by spearheading a program that
collects and recycles waste that they don't manufacture. Subaru is a model for
other companies that want to give back and preserve the environment."
The partnership with TerraCycle's Zero Waste Box™ program is part of the
larger Subaru Loves the Earth initiative, which is dedicated to preserving the
environment.
The automaker's commitment to preservation is one part of the Subaru Love
Promise.
Get the latest insights, trends, and innovations to help position yourself at the forefront of sustainable business leadership—delivered straight to your inbox.
Sustainable Brands Staff
Published Feb 14, 2019 7am EST / 4am PST / 12pm GMT / 1pm CET